Belt Technologies was recently contacted by a producer of commercial offset inkjet printers for help designing and manufacturing a thin, stainless steel print belt. The belt needed to have small perforations that could create an air-separated vacuum; this vacuum would control the movement of paper sheets through the printing press. The inkjet printer was designed for use by large, commercial companies to print books, pamphlets, and magazines on demand—which meant repeatable accuracy was a high priority.
Paper Moves Faster and Easier with Vacuum Technology
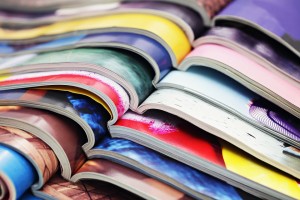
The inkjet printer was designed for use by large, commercial companies to print books, pamphlets, and magazines on demand.
BTI engineers needed to provide a superior printing surface to ensure the smooth, high-speed transport of paper through the machine. The customer’s design called for a thin belt with the dimensions 430 x 0.1 x 3500mm. After experimentation, the thickness was changed to 0.15mm for greater stability and easier handling. The stainless steel print belts were then perforated with thousands of small vacuum holes, each with a diameter of 0.6mm.
Belt Technologies engineers worked with the customer to experiment with vacuum perforation patterns until an acceptable distribution of perforations was determined. The perforations were made using a special cutting procedure with a visual imaging camera. To increase the positional accuracy of paper being transported on the belt, encoder holes were added for straight, optical tracking.
Special Application Considerations for Surface Texture
To ensure the smooth movement of paper through the printer—and to minimize the risk of paper jams—the metal printing belt needed to be extremely smooth and have as few welds as possible. Belt Technologies provided the client with a one-weld belt. Our engineers experimented with the weld angle until they achieved perfect flatness with proprietary inspection procedures and equipment that had been developed in-house.
For this application, the surface texture of the stainless steel print belt would be incredibly important. If the surface of the belt was too smooth or too rough, paper transport would be disrupted and the printer would not function as designed. We have worked extensively with our suppliers to produce steel of the correct roughness.
Collaboration for Optimal Results
We were able to use the knowledge and experience gained from other metal belt applications to provide advice about the appropriate thickness of the belt. We were also able to find cost-effective ways to adapt the printing belt design for the client’s specific requirements. Our engineers worked directly with the client’s technical department from the beginning and made several reciprocal visits to exchange relevant information in person. At Belt Technologies, our goal is to provide you with automation solutions that work; communication is a valued part of that process.
Do you have a unique or challenging automation project that would benefit from the repeatable accuracy of stainless steel conveyor belts? Contact the experts at Belt Technologies, Inc. today!