Curtain coating method for more efficient battery production
ETH Zurich is one of the world’s preeminent universities in the field of technical science and is an educational leader in continental Europe. Representatives from the university’s Institute of Electronics recently approached Belt Technologies for a new research project in battery production. They wanted to find a faster—and therefore more cost-effective—method to apply liquid coating during the production of batteries. They turned to us for a stainless steel belt conveyor that could withstand caustic chemicals and high temperatures, while evenly applying a liquid “curtain coating.”
Source: https://www.sciencedirect.com/science/article/pii/S2589004221000237
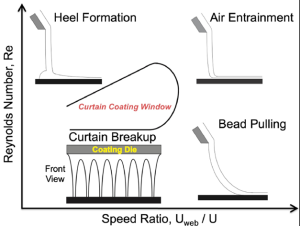
Curtain coating process
Source: https://www.sciencedirect.com/science/article/pii/S0377025717305554
Why Curtain Coating?
When it comes to the manufacturing processes for the liquid coating of surfaces, curtain coating has the potential to overcome the production speed of the currently used slot-die coating method (also known as slot nozzle coating) in battery production. Like the standard method, the curtain coating method allows the active materials, known as anode and cathode materials, to be applied as a paste to an aluminum and copper foil to produce the batteries.
The Search for a Solution
In this instance, the challenge was to find a suitable conveyor belt that was not only hygienic and easy to clean but could also withstand aggressive chemicals and high temperatures for drying. In addition, the customer required a low-vibration run to not only transport the battery components safely and accurately, but also to apply a uniform coating.
Conventional flat belts were out of the question due to their decomposability through chemicals and particle generation. After a long search, the customer discovered a picture of an endless steel conveyor belt for chocolate production and came looking for us. After an extensive examination of their setup, we determined that a PureSteel® endless metal belt would be the optimal transport solution for the curtain coating system.
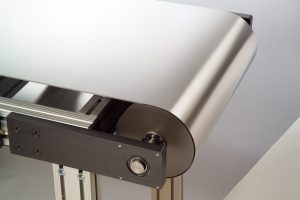
PureSeteel-enldess-metal-belt
Throughout the development project, constant cooperation and communication between Belt Technologies and ETH Zurich led to the delivery of the desired belt, as well as the associated drive and deflection rollers made of aluminum with anodized hardness coating, which were installed in the transport unit designed by ETH Zurich.
Battery quality depends on a precise and error-free coating. Because of this, the fluid-dynamic properties of the paste had to be adapted per the new method. Therefore, the team carried out a CFD simulation of the coating to further investigate the fluid-dynamic behavior of various liquids at the impact point, as well as a laminar distribution over the carrier material. For the experiment, the liquids were applied using a slot-die method and different coating thicknesses were determined based on the different speeds of the belt. The results of the investigation served as a “proof of concept” of the curtain coating method’s ability to enable improved cycle times.
Due to the extremely positive results, it can also be concluded that thanks to the flat and robust steel belt, thinner and less stable current collectors (foils) could be selected for the coating. This would allow for a reduction of “dead weight” in the battery.
Source: https://www.sciencedirect.com/science/article/pii/S2542435121001501
The Search for a Solution
In summary, the project determined that the curtain coating method—in combination with the PureSteel® endless metal belt—can enable chemical, thermal and mechanical stability with simultaneously increased production speed and better cost efficiency for battery production.
If you think you could benefit from one of our PureSteel® products or our engineering expertise, contact our sales engineers today.
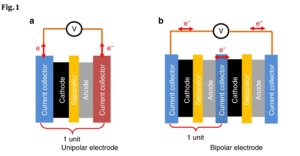
Typical battery design